The use of metals in aviation dates back to the early 20th century when aircraft were first built with lightweight but fragile wood and fabric. The introduction of aluminum in the 1920s revolutionized aircraft design, offering a lightweight yet strong material ideal for airframes.
As aviation advanced, the need for materials that could endure extreme temperatures and stresses grew, leading to the development of high-strength alloys. By the mid-20th century, titanium and superalloys emerged as critical materials, enabling the construction of jet engines and supersonic aircraft. These innovations laid the groundwork for sophisticated materials, and each aircraft engine requires a highly specific and precise metal composition. Companies like Techjet that supply those components must employ highly qualified personnel, specialized knowledge in metrology, and dedicated advanced metallurgical labs.
Metallurgy and Aviation Manufacturing
Metallurgy is the science of metals, focusing on their extraction, processing, and adaptation for specific applications by understanding and manipulating their physical and chemical properties.
In the aviation industry, metallurgy is indispensable. Aircraft components are subjected to extreme stresses, high temperatures, and corrosive environments, demanding strong and lightweight materials.
Aviation manufacturing relies heavily on advanced metallurgical processes to create components with these mechanical properties. This includes the production of jet engines capable of withstanding intense heat and pressure, as well as aluminum and titanium alloys that form the backbone of airframes. The application of metallurgical science ensures that these materials perform reliably, enabling safer and more efficient flight.
The Science of Aerofoil Manufacturing
The journey of aerofoil manufacturing is a complex process that blends metallurgy, engineering, and precision. It begins with material specifications alloys that meet specific strength, weight, and heat resistance requirements. Metals like steel, nickel, and titanium are chosen for their ability to withstand the stresses of high-speed flight and engine operation.
The next step is forging, where powerful hydraulic presses shape raw materials into preliminary forms. This process enhances the structural integrity of the materials through unique grain flow patterns, imbuing them with the strength required for aerospace applications. Once forged, the components undergo heat treatment to achieve optimal material properties. Using vacuum ovens to prevent contamination, precise thermal cycles improve the metal’s tensile strength and resistance to fatigue.
Following heat treatment, precision machining refines the components to exact specifications, ensuring aerodynamic efficiency and structural reliability. Each production stage undergoes rigorous testing, including non-destructive inspections and metallurgical lab analysis, to validate mechanical properties and detect potential flaws. This commitment to quality ensures that every airfoil performs flawlessly under aviation’s extreme demands.
Pioneering Resilience in Aviation
Techjet’s expertise in manufacturing extends beyond forging and heat treatment to encompass a full spectrum of advanced processes. “Our forging processes ensure unparalleled strength and reliability,” says Eyal Erez, CEO of Techjet. “It’s this precision that allows us to meet the high demands of modern aviation.”
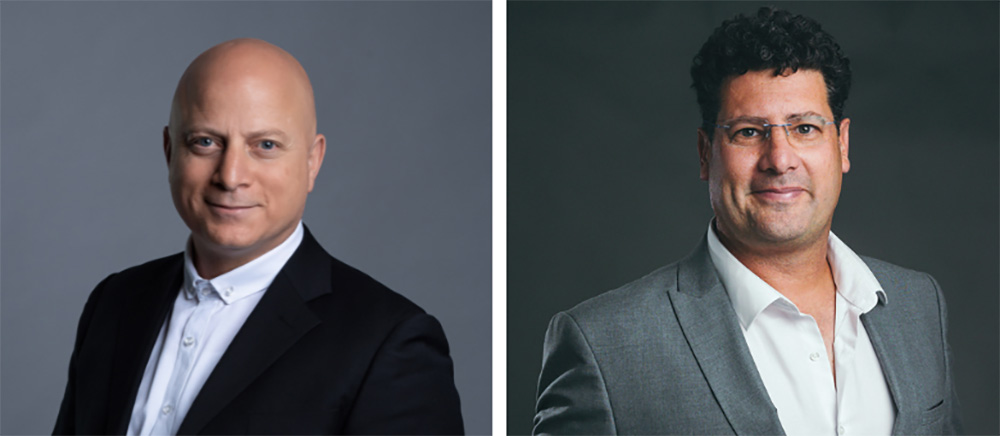
Techjet: Eyal Erez, CEO, Kfir Sharon, VP of Business Development
In addition to forging, Techjet’s vacuum ovens deliver the precision needed for high-performance components. “Heat treatment is where good materials become exceptional,” adds Kfir Sharon, VP of Business Development. “It’s not just about science; it’s about meeting the needs of our clients and delivering solutions that last.”
By integrating client feedback into its production processes, Techjet maintains a customer-focused approach to innovation. Understanding its clients’ challenges drives the company’s technological advancements, ensuring its products remain relevant in an evolving industry. “Our innovation is driven by our customers,” says Sharon. “Their challenges inspire us to think beyond current limits and create the solutions of tomorrow.”
The company is embracing innovation alongside delivering top-quality jet engine compressor blades by optimizing quality checks and utilizing specialized manufacturing processes to ensure accuracy and safety at the highest standards. Sharon believes the next decade will bring transformative changes to aerospace materials, and Techjet is determined to remain at the forefront. “Innovation in aviation isn’t optional,” says Sharon. “It’s how we ensure our clients’ success and our industry’s evolution.”